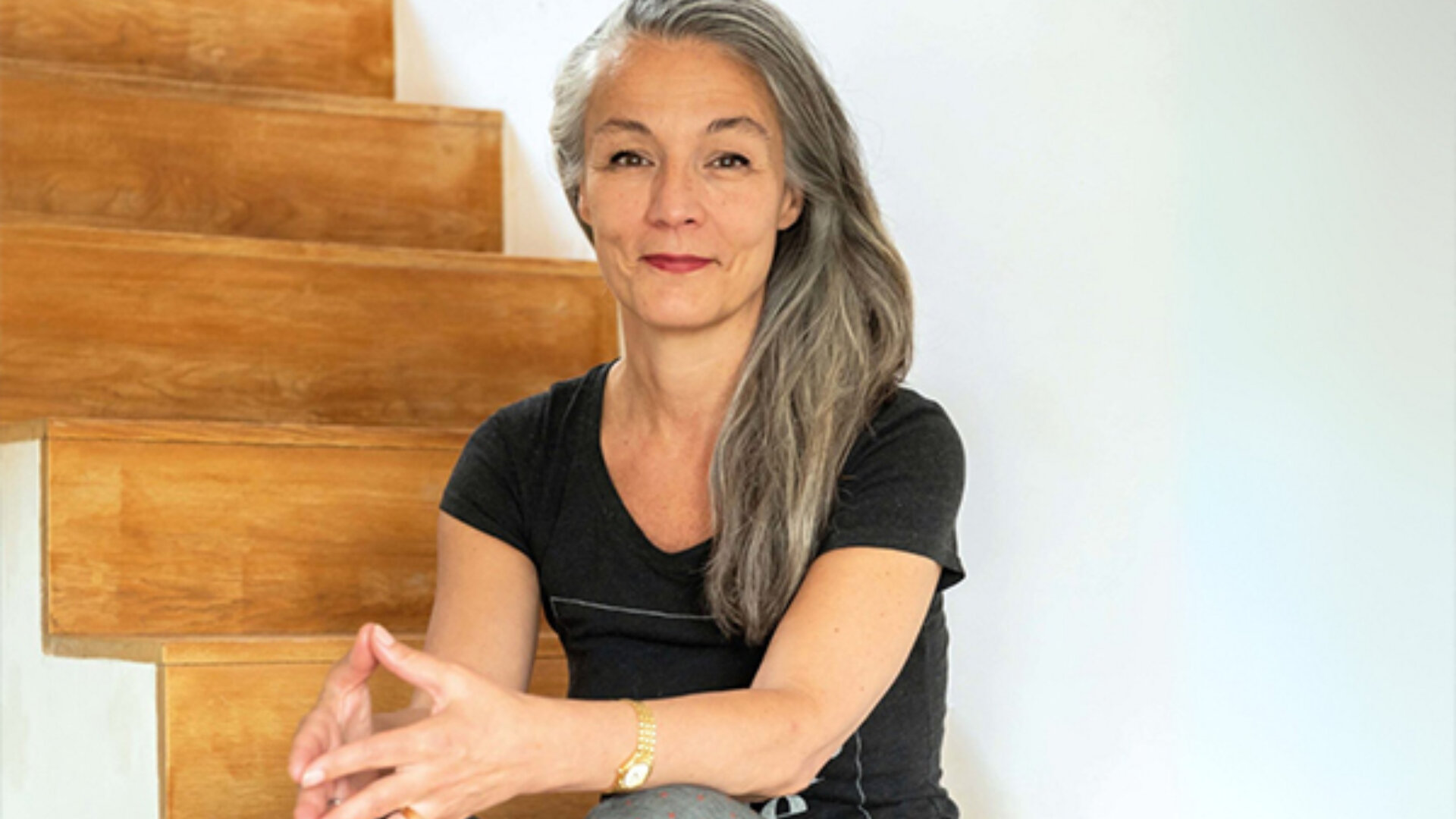
10th April 2025
A life mission in decarbonising spaces: in conversation with Sasha Krstanovic
Sasha is the founder of mstep, an engineering design consultancy that specialises in decarbonising spaces. Cagni Williams likes to work with engineers who are committed to building a more sustainable world and for this reason we have worked with Sasha Krstanovich for almost two decades. When she established mstep, we were pleased to support the new venture by immediately inviting her to work with us on our projects. Mstep has delivered cutting-edge technology designs to decarbonise and bring in energy efficiency in private homes through heat recovery systems. Thanks to Sasha, we gained in-depth knowledge of Ground Source Heat Pumps (GSHP) and were introduced to Chris Davidson, the Chairman and CTO of Genius Energy Lab. Together we are working on the Sidney Street heat Network project.
As part of our “In conversation with” series we find out the origins of this passion and share valuable insights on addressing scepticism.
Sasha has almost 30 years’ experience in design and building engineering and is a Fellow of both the Institution of Mechanical Engineers and the Chartered Institution of Building Services Engineers. Her focus is on low energy and zero carbon building design. She is currently MEP technical advisor to the UN for the restauration of the Palais de Nations, the UN’s Office in Geneva.
As a regular speaker at conferences on low-energy and low-carbon building design, Sasha shares her expertise in this vital field. In 2021, she won the CIBSE Engineer of the Year award and became a CIBSE Board Member in 2025. As the design lead for mstep, Sasha oversees the design and delivery aspects of all projects, actively participating in the early stages and attending key meetings through to a successful handover.
LCC: Low-energy buildings are more than just good design. They are about execution. What is the role of the MEP engineer to ensure project's low-energy goals are actually met?
SK: The only way is to keep the MEP engineers on board until handover. There’s no other way. What often happens, especially in projects perceived to be of lower value, is at completion of RIBA stage 3 or 4 clients passes the project to the contractor to implement. Of course contractors are essential but with low-energy and slightly more thought-through MEP systems, will find contractors not used to this type of work and therefore not confident doing it. They are going to try to change the designed systems with the excuse of saving time and money.
LCC: Contractors might also be worried about being sued, or that client will complain about the building not being warm or cool enough.
SK: Their job is to provide the equipment and installation to the specification they were given. And if they have done that, they are completely fine. Complaints can come to us if what we specified doesn’t work.
LCC: Regarding retaining the engineer until handover, have you done or do you do post-completion evaluations on all your projects?
SK: That’s a very good question. Personally, I love going back to my projects post-completion. We get follow up projects because we stay in touch with clients and ask a lot of questions. Usually, the design team moves away from projects when completed. We, on the contrary, want to know how projects evolve, how buildings are used and find out the reason why predicted energy figures might be different from the actual if they are. Post-occupancy evaluations though are quite involved processes. To be done properly, they require a team’s work for several for several days, which somebody needs to pay for. So, whilst I will ring up a client and say, "How is it going?" then find out it might not be working because they have switched something off, a proper evaluation takes time and costs money, it is nonetheless a worthwhile investment.
LCC: Are clients not ready to make the investment? Isn’t it a good idea to understand if systems work as designed?
SK: Public sector clients, for instance, have an obligation to carry out “Soft Landings” process which is a strategy adopted to ensure the transition from construction to occupation is ‘bump-free’ and that operational performance is optimised. It is carried out throughout the design process and the evaluation consists in a comprehensive look into the building, seasonally commissioning it, going back, checking what is doing, and then at the end, comparing notes, going hand in hand with the building defects assessment process. After completion then the building is still assessed and evaluation about its set up is been carried out. This is an expensive process, something between £15K and £50K and more. People don’t want to do it because they don’t see the value.
LCC: Do you think it has value?
SK: I don’t think it needs to be that complex in every instance. In the same way that we do the surveys when we go look at a prospective retrofit, we could also go back after 12 months and do an end-of-defects inspection and see what’s going on, or halfway through, and so on. But it still takes time and somebody needs to commit some funds to get the team to return. We are currently involved in improving the performance of the building I originally designed MEP for 20 years ago. After many years of the building being operational, the client wanted to replace the entire ground source heat pump plant. They had an open-loop system, and wanted to replace one plant room and put in a new one to eliminate gas-fired heaters. We proposed to connect them to the new ground source heat pump with two pipes. Simple. When I got the drawings from the contractor, they had proposed air source heat pumps to heat the water disregarding the substantial GSHP investment in the same building, on the same level, on the roof, producing more than sufficient heat. So no need for an extra air source heat pump! But then, everyone has their reasons and they need to be discussed, which is why it is essential to retain the MEP designers until handover.
EW: Sasha, what’s the answer to people asking for resilience in their systems? With air source you might design N+1 units, to have an extra heat pump if worried about one failing. Is it the same for ground source? Are clients worried that the ground source loop will be dug up by somebody? How do you deal with that?
SK: With a closed-loop system (close circuit, no water taken from underground aquifers), when the borehole is drilled, two loops can be installed into the same hole, so one is always spare, i.e. two bits of pipe. These are all pressure-tested. So if somebody shoves a drill through a loop and breaks it, there’s another loop in the same hole.
For open-loop systems, as it is using water from underground aquifers, clients tend to worry about the continuous availability of natural water and they have to accept that rivers and underground waters have always been here, aquifers have always been here. The only real risk is if there is a major drought. But that hasn’t historically happened. And if it does happen, then we’ve got a much bigger problem than just losing a bit of cooling or heating.
LCC: Is that why Specialist GSHP engineers prefer to put closed-loop rather than open-loop?
SK: I think closed-loop system are easier in terms of logistics, though more expensive. To get an open-loop system, you have to engage in a long discussion process with the Environment Agency and then wait for approval. It’s quite an involved process. You also need to do test bore holes. If you hit the wrong place, you might get no flow at all. It’s a bit of black magic and contractors really don’t like it. In 2020-2021 we were working on a University building in Central London. Until we got specialists involved the contractor failed to produce factual information during the test —saying there was no water at all for an open-loop system. That was subsequently proven wrong by the specialist and the building has been operating happily since.
In urban rather than rural settings, it’s incredibly hard to get open-loop off the ground just because of the logistics and the length of the approval process.
EW: About air source you would have one extra more machine for resilience, and air never runs out in terms of your energy bank. But before we had air-source heat pumps—so, 10 to 15 years ago—did big buildings use gas or oil for cooling or heating?
SK: This is a really interesting point you just made. We’ve always had heat pumps. Since the Willis Carrier came up with a unit in 1922: they’re called chillers. Since day one, all commercial cooling has been done via heat pumps. That’s what a chiller is, powered by electricity.
EW: So chillers were also electric…
SK: Same as heat pumps. It’s exactly the same technology. Nothing has changed. The really interesting thing is that we have always had reversible chillers—chillers that could both heat and cool. That’s what people now call heat pumps. Actually, they are not just heat pumps—they’re reversible heat pumps, meaning they can switch modes by reversing the direction of the flow of refrigerant. Because heating with heat pumps hasn’t been very efficient, buildings in London always had gas or oil-fired boilers for heating and chillers for cooling. Ground source is better because air is volatile and chillers have temperature drops, ponding from condensation, and ice-ups on the fins of the heat exchangers. That’s why air-source heat pumps have been less developed. It is not because the technology itself is different, but because air is a volatile medium for heat exchange whereas the ground is stable.
EW: So now we’re moving to reversible heat pumps that can heat or cool using a ground array. But I’m still trying to crack the resilience issue. Is it because there is a ground loop running across all the boreholes that could get dug up by someone? Is that the concern?
SK: None of these things are a problem. That’s like saying we have a high-voltage cable in the ground! If someone digs it up, we’ll have an explosion that affects half of my neighbourhood. It’s the same level of concern. With open-loop, if you have a license, it’s on the map so nobody can just steal your water. That’s the whole point of licensing. The issue is hearts and minds, getting people to accept it.
LCC: We recently launched Cagni Williams Energy to help de-risk and implement fifth-generation energy systems at scale. From your perspective, what are the biggest barriers to widespread adoption of this technology? And how do we overcome them?
SK: Well, apart from what we've already talked about, the big barrier is infrastructure. Laying pipes in the ground is disruptive. Ask anybody who's ever tried to do it. It shouldn't be, but every utility company is governed by a different set of rules. Sorting out the infrastructure—actually putting the pipes in the ground—is difficult. The other issue is perception. Everything else is easy. It can be demonstrated as cost-saving, emissions-saving, and valuable. But ripping up the streets? That’s the challenge.
LCC: Ground source heat pumps have been a key part of your work. When did you first become interested in them, and why do you believe they're the best solution today?
SK: In 1981, because my dad said so, seriously. He came back from a congress in a Nordic country and couldn't stop talking about ground source heat pumps. He explained to me in a way that made sense, why they are more efficient than anything else. That stuck with me. Then, when I started looking into it more, it made even more sense. It goes back to engineering logic. Like you said, Edward, if it lifts the temperature a little or lowers it a little, that is more efficient.
LCC: If you could change one major policy or industry practice to accelerate the adoption of sustainable or low-energy buildings, what would it be?
SK: I would speed up the way EU taxonomy is implemented in all European countries, especially the UK. Taxonomy imposes strict limits on emissions, and anything that exceeds them is heavily penalized. So big investors such as pension funds with large real estate portfolios are actively reviewing their holdings to ensure they stay within their allocated quota because anything above that costs them dearly. EU taxonomy already applies in many European countries, as the legislation is out there already, so it just needs to be implemented by all companies operating in the EU, and if so it will cover the UK too very soon, this means investments, operational costs, and carbon footprints are and ewill be more and more scrutinized, even for SMEs.
LCC: Someone told me that in the Netherlands, there's already a set kilowatt-hour limit. That’s it—they can't go beyond that?
SK: Yes, not just the Netherlands. The whole EU—it started two years ago.
LCC: But not all countries have implemented it yet.
SK: They have to. It’s EU-wide. What people in the UK don’t understand—or try to ignore—is that companies that operate both in Europe and the UK are subject to it. Since they’re EU-based, their UK investments also come under scrutiny. For example, we looked into decarbonising buildings in Hungary owned by a large global bank. It’s all about getting buildings to an energy level that the grid can handle by the 2040–2045 zero-carbon transition. If buildings switched to the grid now with their current energy use, the grid would fail. It’s that simple. In the UK, the GBC is addressing this. We’re gradually reducing energy use, aiming for 60–80 kWh per square meter annually for commercial buildings. This is what the grid can sustain renewably by 2045–2050. Currently, buildings coming online in the UK are at 200 kWh per square meter. That’s three or four times more than we are aiming for and it’s ridiculous because, in 15 years, these buildings will be illegal. But they’re still coming straight from design desks now.
LCC: Boston and New York have done something similar to the EU They set a maximum energy use limit, and if buildings exceed it, they get massive fines.
SK: It will happen here too—sooner than people think. But right now, developers have carte blanche to build inefficient buildings that will just have to be retrofitted soon.
LCC: Thank you Sasha for sharing your knowledge and experience with us. Cagni Williams Energy looks forward to continue our strong collaboration with mstep, working together towards a more energy efficient and sustainable built environment.